When the mold heating tube operates at high temperatures,there are strict requirements for the structure of the matching cables.High-temperature resistant cables need to possess properties such as heat resistance,oil resistance,bending resistance and stable insulation to ensure the long-term safe and reliable operation of the entire heating system.
The common mold heating tube matching cables adopt silver-plated copper core conductors,which have excellent electrical conductivity and high-temperature resistance.The outer layer of the core wire is covered with glass fiber or fluoroplastic,effectively isolating heat source radiation and external wear.Some structures are also equipped with silicone layers to enhance flexibility and fire resistance.
The insulation layer design is one of the key structures.Fluoroplastic insulation layers can withstand continuous working temperatures above 200℃and are widely used in mold heating tube systems that require high power density heating.For scenarios that require frequent movement or multiple bends,adding a high-temperature elastic rubber layer can effectively extend the service life of the cable.
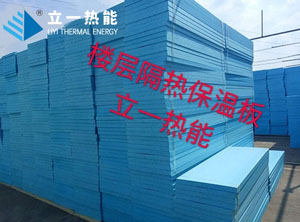
The sheath material is mostly made of silicone rubber or glass fiber braided material,which has both wear-resistant and anti-aging properties.The thickness of the sheath should take into account both mechanical protection and cable heat dissipation to prevent local heat accumulation from causing insulation failure.Some of the heating tubes for molds are equipped with stainless steel flexible hoses or mesh sleeves for the cables,which are used to enhance the overall anti-interference ability and mechanical strength.
The connection terminal part should use crimping structure or special high-temperature resistant connectors to avoid poor contact or oxidation and peeling problems caused by long-term heating.The end treatment should be covered with an insulating coating to prevent leakage and breakdown risks.
High-temperature resistant cables with reasonable structural design can effectively reduce the failure rate during the operation of the mold heating system.When selecting cables for mold heating tubes,it is necessary to clearly define the voltage level,working temperature,wiring radius and usage environment to ensure that the structural parameters of each part are matched,thereby ensuring the long-term stable operation of the entire set of equipment.